Photoelectrochemical Hydrogen Production on Textured Silicon Photocathode
전체 글
수치

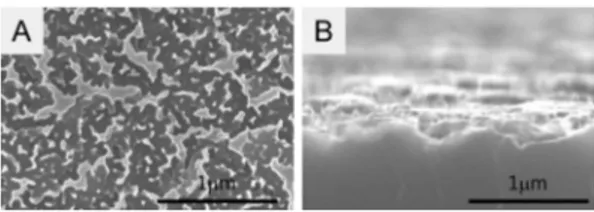
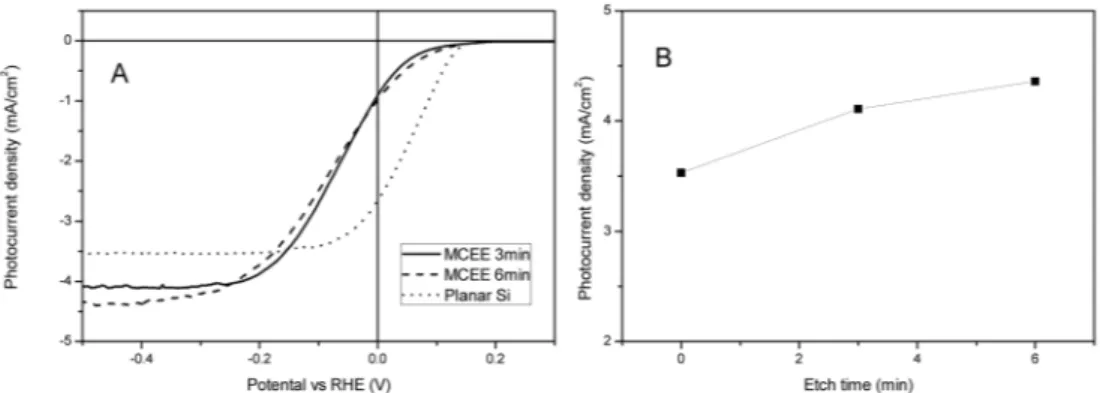
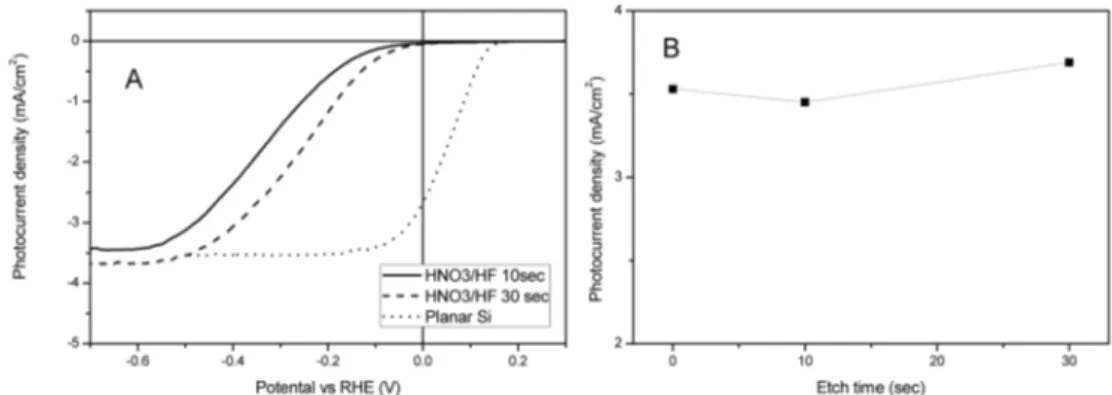
관련 문서
In the hydrogen production by steam reforming of LNG, the catalytic performance of NA and M/NA catalysts was well correlated with the nickel surface area of the
1. Prismless layer was commonly observed on the fissure enamel in young and mature premolar. There were no differences in micro-structure and etching
Discontinuum Continuum.. and Min, K.B., 2015, Discrete element modeling of transversely isotropic rock applied to foundation and borehole problems, 13 rd ISRM
Photoluminescence properties and surface morphologies of porous silicon were investigated by controlling of etching times and applied current densities..
K., "Hydrogen production by catalytic decomposition of methane over activated carbons: kinetic study", International Journal of Hydrogen Energy, Vol...
Plasma는 강한 산화/환원성을 가진 재료로 구성되며 일정 압력 하에서 다양한 방법으로 가해지는 전계(Electric Field)에 의해 기체 상태로 가속된 입자가 되어 식각 대상 재료와 만날
Recently, metal-assisted chemical etching (MACE) has been widely used for the synthesis of SiNWs, because this technique has advantages such as simplicity, low operating
J., “Hydrogen production from partial oxidation of dimethyl ether using corona discharge plasma”, International Journal of Hydrogen Energy , Vol.. Liu C.,